In recent years, organizations are well aware of modern techniques and methods to implement quality management and adopting advance systems like total quality management, lean manufacturing, material flow cost accounting etc., to enhance capability of individuals and processes. 5S is one of most widely opted techniques is commonly used among the organizations from various segment in the world in order to enhance productivity and human capability. It is commonly studies that implementation of 5S methodology could considerably raise the health, safety, housekeeping as well as environmental performance in manufacturing facility. Because 5S methodology and its processes are dedicated to cleanliness and standardization in workplace through structured program to systematically achieve well organized workplace, as result you can achieve safer, efficient and more productive workplace.
What is 5S Methodology?
“5S Methodology is work culture practices for maintaining workplace organize by a systematic and disciple method that uses an acronym of five Japanese works which stand for Seiri (Short), Seiton (set in order), Seiso (Shine), Seiketsu (Standardization) and Shitsuke (Sustain).”
5S mean, Good housekeeping techniques for enhancing productivity, quality and safety at the workplace. Many organizations are already practice the 5S and achieve significant benefits from effectively implement all stages in workplace. If you are implementing total quality management or lean manufacturing, you have to initially and fundamental step implement as 5S to track the continuous improvement as operational level.
Why good housekeeping?
[ 1 ] A neat and clean workplace has higher productivity.
[ 2 ] A neat and clean workplace meets delivery deadlines better.
[ 3 ] A neat and clean workplace produces fewer defects.
[ 4 ] A neat and clean workplace reduces the cost by reducing inventory.
[ 5 ] A neat and clean workplace increases morale of the employees.
[ 6 ] A neat and clean workplace is a much safer place to work.
But, 5S is more than housekeeping, it is system to reduce waste and optimize productivity through sustaining a systematic workstation and using visual indications to achieve more stable operational results, because operational stability require for making and sustaining continuous improvements in workplace.
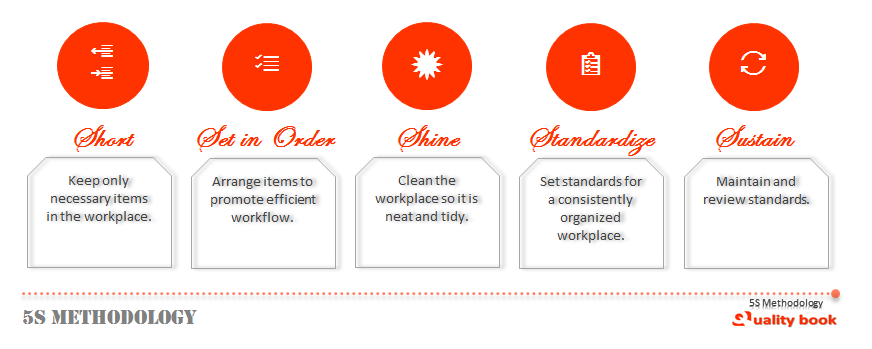
Elements of 5S
5S methodology represents five basic disciplines for maintaining a visual workplace which is foundational to continuous improvement and manufacturing strategic concept to removing waste and well organize manufacturing facility. The five stages – shorting, set in order, shine, standardize and sustain that are also known as 5 elements of a visual workplace. So, let’s see all five elements of 5S:
- Short– Short our items and discard the unnecessary.
- Set in Order– A place for everything and everything is in its place.
- Shine– Clean your workplace thoroughly.
- Standardize– Maintain Standard.
- Sustain– 5S is a habit and is continually improve.
How to effectively implementation 5S Methodology?
- Very first you have to understand manufacturing and supporting processes, production stages, process flow, and material used in processes, identification of plants resources to mapping 5S implementation at various locations.
- Identify a pilot locations and educate everyone working in that area on 5S Methodology.
- Define 5S system’s implementation related objective as company object and include safety, and quality as on initial implementation parts.
- Try to make the facility visual and make the workplace easy to use.
- Brain storming for new methods to make work easy.
- Everyone is responsible for its location, machine and workplace, define responsibility of key personnel.
- Maintain activities according to standards, in case of any mistakes correct immediately.
- Identify root causes by 5 why method.
- Live 5S daily basis, sustain the 5S methodology.
Core Team
To effectively implement any system in organization, need to build a strategic method and team to conduct all activities of systems reach at all the level of organization, and establishment of core team is one of the initial step of 5S system.
The core team leads the 5S system process, and involvement of workmen in core team from various workplaces helps to improve floor level knowledge and understanding which is extremely important to manage 5S Methodology tasks from paper to ground level. Because 5S system focus on well-organized workplace, everyone’s opinion, responsibility and authority must be define of core team, and with all the people of workplace are also responsible for support and maintain standards around its work.
5S Methodology elements:
Short
The first stage of the 5S system is short, states to the act of segregate away all unwanted, unnecessary and unrelated materials in the workplace. Simple meaning of this stage is to short out between wanted and unwanted items at workplace and removal of unwanted item. It is also initial cleaning stage where all the unnecessory items are elimination require for better organize remain items.
Why is it important?
- Time, money, energy, space and other resources can be manage and use most effectively.
- Enhance communication between workmen.
- Frustrations and reduces problems in the work flow.
- Increases product quality and enhances productivity.
Implementation Method
- You have to decide what materials / items are necessary and which materials / items are unnecessary or unwanted. To identification of uncecessary items you should not only verify the floor but also at your around your workplace.
- Very important is “Red Tag”, put a red tag on all unwanted items and keep them in a separate location.
- If any item(s) you used once or twist time in 6 to 12 months may located at a distance from your workplace.
- Any item(s) used frequently should be available and accessible at a central point in the workplace.
- Any item(s) are not in used since one year, discard it.
The short refers to the practices of going through all the tools, equipment, devices, materials, papers etc., in the workplace and keeping only useful materials, that you remove all items from the workplace that are not need for current operations and manufacturing transactions it does not mean that you only eliminate that items that you know you may never requirement, materials which is not currently in use it should store offsite or discard.
Red Tag
- A red tag is strategic method of identifying and removing all unnecessary items from the workplace through the use of red tag as a visual control.
- Red tag is simple tag; the goal is to remove nonessential materials from workplace.
It is simply putting red tag for all potentially unwanted materials and moving it into a red tag area, red tagging helps in identifying and disposing unwanted materials with due accountability and authentication.
- See RED TAG example:
The materials / items are red tagged and stored in a red tag area for a specific time period, in case anyone can request for any item if there is anything need otherwise it should be disposes through recycling, trash or resale.
What red tag indicate?
- On which item having attached a red tag indicate this is unneeded / does not belong in the workplace.
- On which item having attached a red tag indicate storage area not specified for this item.
- Red tag indicates, reasons what each item is and why it was tagged which is described in particular field of it.
- The item is moved for particular reasons, and what action processes required on it.
Action on Red Tagged Items: Table
DISPOSAL | SELL OR RETURN | LEND OUT | CENTRAL RE-TAG AREA | DISTRIBUTE |
---|---|---|---|---|
Items that are unnecessary or useless should be disposed / throw it away from workplace as scrap. | You can sell to other companies or local vendors that are not in use, or unneeded for any purpose. if the option available with your supplier, you can return it. | Lend items / materials to other department or division of the organization that can use them on an any operation | Move items to the central red-tag holding area for redistribution storage or disposal. | You can distribute items to any other part of the company on a permanent basis. |
Benefits of Short – 5S Methodology stage one
- Saving in use of Space.
- Removal of excess equipment/parts.
- More space made available in filing cabinets/shelf
- Avoidance of error.
- Easy access to things.
- Eliminate unsafe situations.
- Preventing rusting or damage to material
- Reduced inventory by sale of scrap material / excess.
Audit Checklist for short – 5S Methodology Stage: 01
- 1 ) Do you find items scattered in your workplace, mean are there items such as obsoleted or unused signage and documentation on floors, callings, walls, table etc.., within the area?
- 2) Is there any unnecessary or excess equipment and device? Is there obsolete or duplicated storage in the workplace?
- 3 ) Are their equipment and tools placed on the floor?
- 4 ) Are there boxes, papers and other items left in a disorganized way?
- 5 ) Are there items in the workplace area which require achieving or have exceeded their lifetime?
- 6 ) Is it recognizable which items are marked as unnecessary. Has a Red Tag implementation or similar between conducted or recently concluded?
- 7 ) Are all items sorted out and placed in designated spots?
- 8 ) Are tools and stationary properly sorted and stored?
- 9 ) Is uncontrolled personal equipment / device or belongings in the direct work area? Is there discarded personal protective equipment within the workplace area?
- 10 ) Review and use the item disposition list as the criteria for red tagging, is there red tag included area, mark the location, identify a red tag specific location manager write and post standards and rules for item disposition.
Short
Set in order or systematic arrangement is second stage of 5S system. Set in order / Seiton is A rational, orderly and methodical arrangement of all items we use, re-work or write off. Honestly, peoples say about set in order – “Place for everything and everything in its place”, I think is great quote for this stage.
The goal of second stage of 5S system is every thinks in the right places or set up so that they are readily available and easily accessible for use, its eliminate searching of particular thing needs for current operation. Here three basic fundamentals of this stage are:
(1) Organize items in such a manner that they are easy to available, visible, accessible and easy to use.
(2) Sign / labelling them so that they are easy to find and put back.
(3) A place for all necessary items and everything in its place, no more homeless items.
The core team must come together to analyze the workplace area for further improvement opportunities and understand the situation to reduce sources of waste and mistakes as well as to make the workplace more visually instructive.
Team Focus
The team must focus on some basic points such as given as below:
- At the facility equipment, tools, utility, machinery, electrical system etc.., must be well organized and labeling to simplify tracing.
- Document layout, equipment and supplies.
- Every tools, and utility items must be kept near the point of use, labeled and organized.
- To focusing on safety requirements, every workplace must be provided hazard warning systems, safe working instructions at the point of need. And ensure that, the personal protective equipment is easy to access and ready for use.
- To focus on manufacturing processes, every work instruction must be updated, devices used in processes must be mistake-proofing to prevent human and machine errors.
- Every quality standard must be visually designed & properly displayed as well display examples of which kind of results will acceptable & unacceptable in if visual display if possible.
- For easy accessibly and visual management for inventory, and effective identification of production requirements should be maintained accordingly. Every store room inventory properly labeled and description, quantity as well specific location must be maintained.
Implementation Method
- First of all, you have to decide the right place for everything, or any item you have to put on the rack, cabinet or at any place, reassign spaces if necessary.
- Deploy all materials, devices, tools, equipment etc., at a place specified or allocated to them with proper label.
- Indicate / sign / label or numbers of maximum and minimum to alert in case of over load stock situation.
- Use floor pain marking to define working area, gangways, entry – exit ways, safety equipment, locations etc.., this clearly identifies the location of equipment and also warns people passing by not get too close.
- Maintain standards in color coding, specifically for pipelines, water lines, gas lines etc. for equipment, machinery specific color is also recommended.
- Overhead crane, water tanks, chemical / or any liquid tanks etc., must be capacity defined and marked on visible writing.
- Use display cautions, messages, instructions at proper places at height and written clearly.
Benefits of set in order
- Helps reducing time consumed in searching materials for use.
- Easy to inspect and recognize when material is taken out from their location.
- Creates work effectiveness.
- Creates safety atmosphere.
- Helps in inventory control.
- Improve work place utilization.
- Better identification by using color coding, Such as Yellow – Usable, Red – Unusable
Audit Checklist for set in order – 5S Methodology Stage: 02
- Every workplace i.e. whole organization map / layout must be preparing with identified work area that clearly mentioned gangways, manufacturing areas, storage area, recycling area etc.., because layout also helps to moving large items or moving heavy quantitative items much easier if each space is properly indicated. Verify the same.
- Are there materials, tools, files or any other media arranged in a manner that ensures repetition of storage with no duplication?
- Are storage areas: Racks, Cabinet, Floor etc., clearly identified as specific allocation? Are walkways clearly identified? Are there supplies (labels, tags, bins etc..) identified?
- At facility, maintenance, store, operations etc., plant marking standards determined?
- Is it clearly described which item is currently used in processes? Are there processes to ensure that achieved items are easily retrievable?
Shine
Shine mean clean workplace. Includes the cleaning of everything in the work area and keeping it clean. Bright place where everyone will enjoy working. Keep everything in top condition, so that when someone need to use something, it is ready to be used. But during the cleaning processes it must take care, each member should be equipped with adequate cleaning materials that have been tested to make sure the solution will not harm any equipment, machine or work place. It is expected that treat cleaning as an inspection process, perform cleaning & inspection to understand work environments on daily basis.
Implementation Method
- Determine the goal of shine, set up the targets and focus on area where needs to implement.
- Make the division of total workplace area and allocate responsibility for cleaning for each divided area.
- Decide on cleaning points, order of cleaning, type of cleaning and cleaning aid required etc.
- Setup an effective schedule and assign individuals, as well as display cleaning schedule at appropriate location.
- Prepare proper procedure for continued daily shine processes.
- To focus on safety requirements: every team member who performing this task must be equipped with safety tools and personal protective equipment.
- Check specific equipment targets for necessary repairs and replace anything if need.
- During the perform cleaning processes, make sure the defective conditions such as loose wires, loose bolts and nuts, vibrations, excessive sound, temperature etc., in case found talk with maintenance superior for further actions if you are not belonging to maintenance.
- Move the dust, materials removed during the cleaning from various area store at specified / allocated dump yard.
- Shine and inspect through cleaning every shift.
Benefits of shine
- Good, neat & clean working place motivates for effective functioning.
- Increases efficiency of machines / equipment.
- Extends machine and equipment life.
- Creates safe environment and working place.
- Helps ion identifying the potential cause of problems.
- Helps in developing the skill of operator for doing autonomous maintenance.
- Reduction of wastage.
Audit Checklist for Shine – 5S Methodology Stage: 03
- Are there 5S (Shine) schedules & checking & auditing schedules are defined? responsibility & locations are defined, make sure all workmen know their assignments? Verify individual involvement in the process?
- Are the workplaces, equipment, machinery etc., kept clean & shine and free from uncontrolled waste?
- Determine appropriate cleaning method, processes are prepared? And peoples are follow it? People understand it?
- Are the schedules & planning are performing initial cleaning of targets using the initial cleaning plan?
- Are at information locations and notice boards kept up to date?
- Are floor areas being clean, undamaged, without slippery? Verify to consider safety requirements.
Standardize
This aspect of the 5S focuses on standardization, it is the outcomes that exists when the first three pillars – sort, set in order and shine are properly maintained and constant routine. This stage of 5S, forming a consistent way of implementing the tasks that are performed on a day-to-day basis with all first three stages of 5S. Standardization maintained through:
- Operation Standards / procedures
- 5 minutes 5S
- Visual Control (Example: Warning lights, color coding, labels, etc.)
- Schedules for cleaning / housekeeping
- Inspection / audit and checklists
You have to establish a work environment and structure that will support the modern practices and turn them into regular tasks / habits. The main purpose of 5S’s fourth stage “standardization” is to ensure that everyone in the organization strictly follows the same standard operating procedure, the same names of materials / products, the same name of specifications, sizes, signalization, marking, shape and color etc.
The goal of standardization is to establish best practices and to get each member follow standards during implementation and improve workplace practices accordingly. To effectively implement standardization, you have to define roles and responsibilities for each team member and it must be clearly and consistently applied. The important tasks in the 5S system is 5S communication board, where all the information are needs to display for all peoples of organization, se example picture:
Implementation method
- Prepare documented procedures / operations SOPs, work instructions and guidelines for initial stages such as shorting, set in order and shine for the visual workplace.
- To maintain standards, make the audit checklist for each department, section and division as well as train your people in using them.
- 5S evaluation is one of the important tasks of 5S system, carry out monthly, quarterly or periodic evaluation by verify and using the audit checklists.
- Visual management is best part to implement and to act faster for such as: Labels at each material, tanks, equipment, chemical storage areas etc.
- Identify and categorize a condition to standardize.
- During the periodic 5s evaluation, needs to discover new potential control ideas as floor condition. Choose, test and implement control ideas at appropriate locations.
- Maintain & monitor those conditions and standards defined.
- 5S system related activities should be planned and schedule at the frequency rate necessary to maintain a clean, orderly and safe working environment.
Benefits of standardize
- Proper & Nice Working Areas
- Help in synchronizing the activities of SEIRI, SEITON & SEISO
- Helps in educating the new persons joining the area on standard methods in practice.
- Reduce breakdown and increase meantime between failure
- Reduce the defects & breakdowns, and less scope for errors and scrap.
- Visual management improves work efficiency (5’S’ – News, Poster, Badges, Slogans & celebrating 5 ‘S’ Day/Week.
- Work area looks more organized and safer.
- With better visual and transparency management work efficiency will improve.
Audit Checklist for Standardize – 5S Methodology Stage: 04
- Is the workplace assumed control methods, are there people easily understand and follows accordingly? Is there you found any leakage in standard appearance in workplace? Are all information centers or 5S communication board used as important points for information?
- Is there working environment, climate setup is proper such as temperature, lighting, ventilation, humidity etc.? is workplace is well enough to be clear of heavy dust? Is there lighting angles are properly set to comfort for work?
- Is the first shorting, set in order and shine are being maintained? Are we operating within the rules that setup & agreed?
- All the people working in workplace are wear clothing which is clean and undamaged? Is personal protective equipment worm as prescribed?
Sustain
To sustain means to make a habit of properly maintaining correct procedures. Sustain also means discipline. It indicates your assurance to sustain regularity and to practice first 4s as a way of life. This also requires that your employees’ demonstration optimistic attentiveness & overcome resistance to change. The stage focus that the 5S mentality is embedded in routine in works and procedures. Some simple points that helps to understand & implement procedure for 5S – sustain:
- Establish the rules to keep the workplace well organized & ordered as well track by established upon standards.
- Ensure that all the workmen, staff, operators and support team must be trained for 5S procedures, work instructions, safety instructions and operational procedures.
- Establish proper structure of how and when 5S activities will be implemented.
- Formulate guidelines for evaluation / audit of 5S implementation.
- Educate and encourage participation through 5S concepts and skills development, 5S communication Boards, emails, visual displays, study groups and weekly 5S activities.
- Draw up and audit system including checklist for 5S for all the workplace, offices, shop floor, storage areas etc.
- Conduct periodic audit and monitor the scores through radar charts / bar charts.
- Appreciate by awarding, appreciation to best workplace, offices, zone etc.
5S audit processes must establish into practice to ensure that all the stages of 5S are properly function and maintained workplace organized as top priority as well as ensuring that the routines & schedules are conducts as specified standardization.
Benefits of sustain
- Promotes habits for complying with work place rules and procedures.
- Creates healthy atmosphere and good workplace.
- Improves Safety and Hygiene
- Improves morale of employees
- Develops team work
- Develops ability to think and analyze causes for improving control system.
- Improvement of Company culture, rules, safety devices, etc.
Audit Checklist for Sustain – 5S Methodology Stage: 05
- Is there sustaining plan is prepare? And ensure that management support for the plan?
- Whether everyone in the workplace area know about the 5S standards and their purpose? Are people within the workplace training in key procedures and practices as well? Are there all the procedures are update regularly and reviewing?
- Is there all equipment, tools, bill of materials, information, files, etc., are store correctly?
- Is there 5S communication board and other communication devices are set and update regularly? Is there information is easy for understand and readable?
5S Methodology Audit
In the 5S methodology, audit is important part of the whole system to ensure that processes are establish during all 5 activities, standardization continues to be maintains. To sustain all 5S activities in organization need periodic monitoring through audit scores, share information on 5S communication board to declare results of improvements. 5S audit is not just audit, its monitoring and improvement must be involve in audit processes. It also verifies the involvement of employees, and engage them in evaluating area outside their workplace, providing support for other workplaces.
The 5S audit deployment process Flow
- Prepare 5S annual plan (Document: zonal list, Previous 5S score, all shifts record, External visitor comments)
- Prepare 5S audit schedule (Document: List of qualified 5S auditors)
- Define department wise 5S auditor schedule (Including all shifts)
- Display, distribute confirmed 5S audit schedule to the concerned member
- Conduct 5S audit as per schedule
- Is there any audit score less than 90%, prepare corrective action requests records and handover to department leader?
- Submit corrective action report with action plan and verify disposition / corrective actions.
- Verify effectiveness of corrective actions taken and timely completion of action decide.
- Is there it is identify satisfactory than close non conformity, otherwise re-request for corrective actions should submit and same processes must be repeating until close non conformities.
5S audit Procedure – General
- Audit Plans
- 5S layer annual audit plan is initial stage of the audit function, generally A 5S annual audit plan may prepare by 5S coordinator to involve all department, sections and workplaces as per define scope of 5S implementation. During the planning section there is two things very important are: (1) scope of the audit – listing department, areas and locations (2) define frequency of the auditors of various layers of the management.
- To cover up all the departments, zone and sections of the organization sufficient auditors must be select and perform its task accordingly. the 5S leader must prepare master list of qualified auditors as well define the auditors’ audit areas to independently each auditor performs its responsibility for the area being audit.
- 5S audit planning is responsibility of Auditors, auditors must verify and review of relevant audit checklist and all previous findings, corrective actions and updated checklist.
Audit Initiation
- 5S audits initially focus on intension of measuring the 5S score in compliance with quality system procedures, work instructions, organization policy, specific checklist and 5S standard.
- 5S auditors shall record all findings in the audit checklist as per list of audit checklists. They shall raise the corrective action report to be provided to the department head in case of any individual score is under the sufficient score line.
- The auditee (appropriate department head) must take action to correct non compliances found during an audit. The department of the audit or non-compliance report shall be sign off by the department head (auditee) upon completion of the planing action & then provide to MR (Management Representative).
- The auditee shall initiate the corrective action with in specifically defined limit of submission of action plan and compliances.
- The 5S representative / auditor will check that the corrective action may require to take & it should effective in eliminating the root cause of the original non-compliance observation and if so, will close out the issue by signing the report.
- 5S representative or auditor will decide, if any more action required at appropriate locations against non-compliance found.
5S Scoring (Simple Scoring) : Table
SCORE | STAGE OF READINESS |
---|---|
1 | Not at All |
2 | Little done in that respect |
3 | It is done but not systematically |
4 | This is being complied with more systematically |
5 | There is an ability to maintain it |
5S Assessment Report: Table
SCORE | PERCENTAGE | ASSESSMENT |
---|---|---|
Less than 30 | Less than 25% | You are not aware about the usefulness of 5S Methodology |
More than 30 & Less than 60 | More than 25% and less than 50% | You are randomly practicing 5S Methodology |
More than 60 & Less than 90 | More than 50% & Less than 75% | You are on the right track. if your score is close to 90 then you have fully implemented first 4S. At this stage your workplace should have a general appearance of orderliness and cleanliness. |
More than 90 & upto 120 | More than 75% & upto 100% | Your management is committed to maintain 5S and employees are showing positive interest in 5S activities. |
Conclusion:
Here I tried to cover all the 6 S = 5S + 1S (Safety) to complete solution for workplace. There is one of the most important is management role in the whole system. Without the management commitment it is hard to implement. By the way 5S Methodology is a methodical process for establishing and maintaining an organize, clean and high performance workplace. If you start or wish to establish 5S system in your organization, you can write me for any suggestion require from me, I will please to help you in this regard.